- UVインキの使用方法
UVインキの使用方法
弊社はこれまで積極的に、紫外線(UV)の照射により瞬間的に硬化して優れた皮膜を形成するUVインキの研究開発を行い、バリエーションの充実を図ってきました。
(弊社商品名:レイキュアーインキ)
そして近年は急速に需要が増えており、これに従いお問い合わせも増えています。
ここではUVインキに共通の一般的事項について、各シリーズのインフォメーションよりも詳しく説明させて頂きます。
1.UVインキの使用方法
(1)室温調整、温度調整
UVインキは、温度の違いによる粘度変化が大きいという性質(高温:低粘度、低温:高粘度)があり、この粘度変化は印刷適性や膜厚に大きな影響を及ぼします。
一般的にインキ温度が下がると粘度が上がり膜厚が厚く印刷され、インキ温度が上がると粘度が下がり膜厚が薄く印刷されます。
またインキ粘度が高くなりすぎて紗の通過性が悪くなると、発泡やピンホール等の抜け不良の多い印刷仕上がりになってしまいます。
従って印刷の際はなるべく室温を18〜25℃位の一定温度に調整して下さい。
マットクリアー、RL厚盛メジウム及びハーフトーン色インキ等は、印刷の再現性を重視するためにチキソトロピック性でかつ高粘度に調整してあります。
この為冬場には室温とインキ温度が適当でないと、印刷が出来なかったり膜厚になりすぎて硬化性が不良となることがあります。
逆にレベリング性・透明性を重視したタイプのインキや高速印刷性を重視したタイプのインキは、夏場に粘度が低くなりすぎることがあります。
一部シリーズのインキは、印刷作業場の湿度が高いとインキが吸湿して、増粘やゲル化などのトラブルが発生する事があります。
このような場合にはエアコンや除湿機の使用により対処して下さい。
(2)スクリーン版
一般の有色インキを印刷する場合には、スクリーン版は300メッシュ以上でゾル厚が10µm以下の版を使用して下さい。
この場合のインキ膜厚は10〜12µmになります。
又印刷面積は約70〜90/kgになります。
一方クリアー類は、低メッシュ版を使用して厚膜に印刷しても問題ありません。
用途に応じて版を選択して下さい。
又なるべく通過性の良い紗を選んだ方が、発泡やピンホール等のトラブルが避けられます。
(3)スキージ
再現性の良い印刷を行う為には、スキージは硬度65〜80のウレタンスキージを使用し、エッジはシャープにして下さい。
UVインキを使用すると、成分中に含まれるモノマーの影響でスキージが膨潤する事がありますので、研磨やローテーションを行い対処して下さい。
(4)粘度調整
インキは、よく撹拌した後に容器から取り出せば、そのまま使用出来ます。
用途によりインキ粘度を下げる必要がある場合は、レジューサーを添加量10%以内でご使用下さい。
逆にインキ粘度を上げたい場合は、マットクリアー(高粘度、コンパンドタイプ)又はJAR-22添加剤(液状)を混入して下さい。
JA-244、JAR-20等の粉末艷消剤も粘度調整に使用できますが、均一に混合するためには充分な撹拌が必要なので、あまりお薦めできません。
(5)濃度調整
インキの濃度を調整する場合は、メジウム(光沢型)又はエクステンダー(艶消型)をご使用下さい。
(6)光の影響
印刷工程中及び版の洗浄作業中は、版上のインキに直射日光が当てないで下さい。
一方蛍光灯の光は、よほど近くでない限りは問題ありません。
(7)標準硬化条件
各インキシリーズ毎にそれぞれ標準硬化条件を設定してあります。
各シリーズのテクニカルインフォメーションに記載された標準硬化条件を参照して下さい。
(8)予備テスト
実際の硬化条件は、印刷材料や印刷条件等によって変化します。
またUV照射機のメーカーや機種よっても硬化性が違ってきますので、必ず本ラインでの印刷と同様の条件で予備テストを行って硬化条件を決めて下さい。
予備テストの手順は次の通りです。
- テストピースにインキを印刷し、UV照射機を標準硬化条件で通します。
- 印刷面の残留タック、接着性、引掻き性、折曲げ性等の試験を実施します。
- 試験結果が不合格の場合には、満足する結果が得られる様に照射機の諸条件を調整して下さい。
適正な条件が見つかるまで、以上のテストを繰り返して下さい。
尚テストの際には、UV積算光量計で光量測定する事をお勧めします。
(9)プレヒート(予備加熱)
接着性のあまり良くない素材に印刷する場合には、印刷後UV照射をする前に、プレヒート(予備加熱)を行なって下さい。
近赤外又は遠赤外ランプ等を使用し15〜90秒位のプレヒートを行なう事でインキの接着性が著しく向上します。
2.UVランプ・UV照射機
(1)UVランプ
スクリーン印刷は他の印刷方式に比較して厚膜になりますので、高出力ランプを使用して下さい。(120W/cm以上)
またランプハウスは、より高い紫外線強度W/cm2が得られる、焦点のある収束型を選定して下さい。
並行型、拡散型のランプハウスでは、積算光量J/cm2は収束型と同程度になりますが、紫外線強度が著しく低くなってしまいます。
ランプの種類は、高圧水銀灯、メタルハライドランプのいずれも使用可能ですが、弊社では積算光量の点で優れたメタルハライドランプをお勧めしています。
(2)UV照射機
UV照射機には空冷型と水冷型があり、どちらのタイプも使用可能ですが、空冷型の方がメンテナンスが容易です。
但し、空冷型は照射時の温度が高くなる傾向がありますので、重ね刷り適性(特に層間剥離)の問題や、プラスチック素材の熱変形トラブルが発生する危険性があります。
印刷素材にプラスチックが多い事と重ね刷り適性等を考慮すると、空冷型を使う場合にはコールドミラーやIRカットフィルターの併用をお勧めします。
(3)UVランプの寿命
UVランプには寿命があり、またランプの光量も徐々に低下します。
時々UV光量計で光量を測定するなどのランプ管理を行って下さい。
ランプが寿命に近くなると、インキの硬化性や接着性が低下する等の影響が出てきますので、ランプは早めに交換するようにして下さい。
3.UV硬化に影響する要因
(1)材質の種類と色
紫外線をより多く吸収する性質を持つ材質の種類・材質の色があります。
これらの材質は、硬化を遅くします。
又、同じ種類の材質でもグレードにより硬化性が異なる場合もあります。
(2)インキの色(顔料の性質・調色時の問題)
インキ成分中の顔料の性質・含有量が問題です。
紫外線をより多く吸収する顔料は硬化を遅くし、含有量が多い程この傾向は著しくなります。
従ってUV硬化型インキの濃度・隠ぺい性には限度があります。
又調色をしたときに、それぞれの原色の硬化性は問題ないのに、調色インキの硬化性が低下する事があります。
特に高濃度白と暗色系(黒、藍、他)との組み合わせの場合は注意して下さい。
(3)光重合開始剤
硬化性の向上には、光重合開始剤(硬化促進剤JAR-8、JAR-15)の添加が有効です。
しかし光重合開始剤を過剰に添加すると、かえって硬化性が阻害されますし照射後の臭気も残りますので、指定の添加量を守って下さい。
(添加量4%以内)
(4)印刷膜厚
印刷膜厚が薄いほど硬化性は良くなります。
一般の有色インキは10〜12µmの膜厚範囲内で十分な硬化性能を得られるように設計しています。
この為膜厚が15µm以上にもなると、硬化不良による接着トラブルを起こす事があります。
一方クリアー類は100µm以上の超厚膜でも問題なく硬化します。
(5)紫外線強度W/cm2と積算光量J/cm2
硬化性を判断する目安として紫外線強度と積算光量があります。
紫外線強度は、2-(1)で述べたように、照射機性能のランプ出力とランプハウス形状でほぼ決まります。
また紫外線強度と照射時間を積算したものが積算光量になりますので、積算光量はランプ本数やコンベアー速度等による照射時間によって変化します。
全体的な硬化性の判断は積算光量で行いますが、前項(4)で述べた印刷膜厚方向の硬化となる内部硬化性に対しては、紫外線強度の方が重要です。
紫外線強度が低いと照射時間を増やしていくら積算光量を上げても印刷膜底部の内部硬化は殆ど良くなりません。
このような場合は、ランプの高さを下げるか、ランプ出力を高出力に切り替えて下さい。
(6)照射時の温度及びプレヒート
UV照射時の雰囲気温度は、UVインキの硬化性に大きな影響を与えます。
温度が高いほど硬化性も良くなります。
従って、UV照射の前にプレヒートを行なう事によりインキの硬化性が向上し、接着性も良くなります。
4.注意事項
(1)皮膚刺激性(P.I.I)
UVインキの安全衛生の目安として、皮膚刺激係数(P.I.I)があります。
- 0〜1.9(低)
- 2.0〜2.9(やや低)
- 3.0〜5.9(中)
- 6.0〜8.0(強)
レイキュアーインキは、P.I.I値が1.9以下の成分で構成されていますので低皮膚刺激性です。
しかし、取り扱いに際しては極力皮膚に接触しないように注意して下さい。
もし付着した時には、直ちに石鹸水で洗い落として下さい。低皮膚刺激性のため皮膚に付着したのに気がつかないでいた場合には、体質によっては長時間接触による炎症やかぶれを起こす事がありますので、注意して下さい。
(2)層間剥離
UVインキを重ね刷りする場合に、下層のインキを過剰硬化してしまうと、上層のインキとの接着性が低下し、層間で剥離する事があります。
このような場合には、下層のインキの硬化条件を調整して対処して下さい。
下層のインキは若干タックが残る程度の硬化であっても、上層のインキを硬化する際に同時に下層のインキの硬化も進みますので問題がない場合が多くあります。
(3)熱変形(ディストーション)
UV照射時の熱の影響により、ステッカーや薄いフィルムはカールや変形を起こします。
特に黒色等の暗色系インキは熱を吸収する性質を持っている為、カールや変形を起こしやすくなっています。
対策としては、UV照射条件の調整や冷却システムの検討を行なって下さい。
(4)ベルトコンベアーの網目跡残り
UV照射機を通った後、印刷面にベルトコンベアーの網目跡が残る事があります。
特に黒インキや薄いシート材の場合に起こりやすい現象で、熱のかかりムラが原因です。
ベルトの材質や網目の細かさを変更するなどの方法で対処して下さい。
(5)貯蔵安定性
UVインキは、直射日光を避け冷暗所に貯蔵して下さい。
この条件で貯蔵した場合の品質保証期間の目安は、一般のインキで製造後2年です。
30℃を超える様な場所での貯蔵はインキのゲル化や増粘の原因となります。
又一度使用したインキは貯蔵安定性が低下していますので、容器に戻すことは避けて下さい。
(6)撹拌
UVインキは容器から取り出す前に必ず撹拌して下さい。
成分の一部が分離している事がありますが、撹拌すれば均一になります。
又貯蔵中に増粘したインキも、撹拌すれば適性粘度に戻ります。
(7)インキの混合使用
一般に、他のシリーズのUVインキ同士を混合して使用することは出来ません。
(8)製品安全データシート(MSDS)
安全性に関する注意事項等は、各インキシリーズ毎に用意した「製品安全データシート」に詳細に記載してあります。
ご使用に際しては必ず参照して下さい。
NOTICE
UVインキの印刷には、従来の印刷に比べて多くの複雑な要因が絡んでいます。
UV照射機、UVインキ及び印刷条件がシステムとして一体にならないと好結果は得られません。
弊社は各種材質へのUVインキの開発をUVシステムとして総合的に行っております。
各種材質・各種用途に応じた多くのUVインキシリーズを揃えている他、UVシステムとしてのノウハウも数多く蓄積しております。
貴社UVシステムの導入に際しましては、ぜひ弊社にご相談下さい。
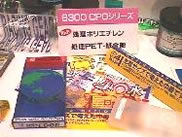
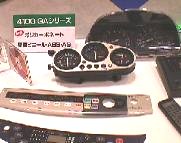
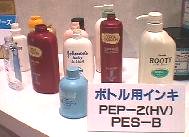
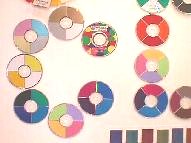