- SPECIAL APPLICATIONS
PRINTING METHOD OF RC UIM 62 SERIES IN IMD PROCESS
INTRODUCTIONS
IMD is currently used moulding method to make mobile phones or electric appliances. RC UIM 62 SERIES is UV curable ink that makes it possible to mould the products with deep arc. This literature shows how to use this ink to obtain successful result in whole IMD process including preliminary-moulding and insert-moulding.
- To anneal the substrate
ayfol is generally used substrate. As Bayfol distorts with heat, it is recommended to anneal this material before printing. The material is heated with UV curing in printing process. Annealing lowers the possibility of printing shear that may happen by the distrotion of the material, which leads to better printing precision.
Annealing conditions : Approx.1 hour at 100°C(212°F, This is appliable to solvent- based ink.) - To print anchor-coating
To print anchor-coating is recommended to improve the adhesion of UIM Ink to the substrate. UIM Ink printed directly on Bayfol would pass cross-hatch test. However, anchor-coating brings better adhesion which may be required of the substrate in moulding process or as finished products.
binder U-1 is good as anchor-coating. Please dilute U-1 by 10-30%by weight of PC thinner and print with 200-250 meshes/inch. Dry the ink at 70-80°C(158-176°F) for 30-40 minutes. - To print images
Images are printed with RC UIM 62 SERIES. Use fine mesh(finer than 300) and make theink film as thick as 10 microns. Too thick ink film causes insufficient curing that degrades the toughness of the ink film.
Curing conditions : Metal halide lamp 120w/cm(peak power:higher than 0.8W/square cm), integral light 350mj/square cm
If metallic color is necessary, use aluminum paste, JA grade. - To print binder
When the resin injected is PC, choose binder G2-S. Dilute G2-S with 10-30% by weight of PC thinner and print with 200 meshes/inch. Dry the ink at 70-80°C(158-176°F) for 1 hour.
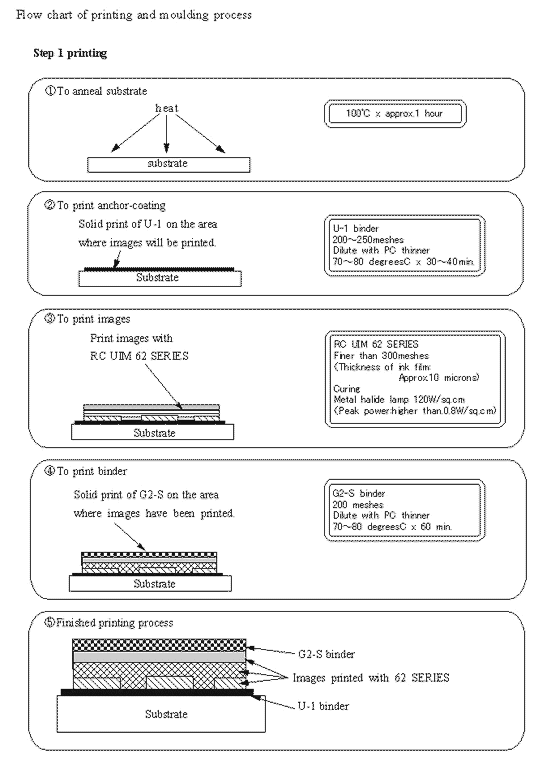
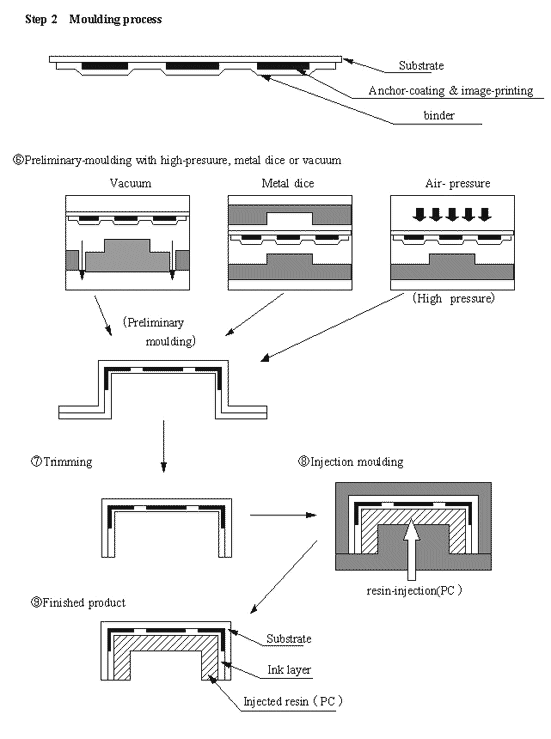